I'm starting out a little late in the thread so here is a quick run down of what I've got so far. I apologize that I do not have any unpacking pics as some of the unpacking occurred at Joe Nall in order to be able to squeeze this thing in the trailer. However from the looks of the box and construction of the fuse I would say that it looks like the planes are coming from the same factory as 3DHS. The included hardware and little odds and ends are identical to what you find with 3DHS along with many extra nuts/bolts. The packaging is top notch as well and the plane is very well protected and arrived with hardly any wrinkles. The plane also comes with what appears to be a 6" Omega Carbon Fiber Spinner (no bolt though so you will have to supply your own, I believe
@vegasking or
@SupaTim carry the right length bolts or you can also source from local hardware stores, should be 5mm x ~115mm long). The plane also comes with some nice cloth wing and stab backs embroidered with the AJ Aircraft logo. One thing not to forget before you throw your box away is the hinge pin for the rudder, you will find it taped to the inside of the box with the fuse. I'll get some pics of this stuff at a later time.
Engine Mounting:
Prior to mounting any gear, I stood the fuse up against the wall and centered the engine up to the cowl. I will be using the 1" blazing star mount that I already had on hand. The mount actually measures out to be 1.125" where as the supplied 1" stand offs will work as well. I ended up having to send my 120 in for a check up but was able to get the firewall drilled and checked for alignment. The pic below shows a DA100 drill guide supplied with the kit. Due to the extra length of the blazing star mount and the right thrust built into the firewall, my mounting holes are shifted by about 1/32-1/16 of an inch as seen in the photo below. If using the supplied stand offs or a true 1" mount, you should be pretty spot on to use the included guide.
Landing Gear:
Next thing I did was prepare and install the landing gear and gear cuffs. I can honestly say this is the first arf I have put the landing gear and cuffs on without cussing or having to modify axles/wheel pants to get everything to fit the way I want it. Again no pics of this step but it is pretty straight forward. The wheels supplied are very nice with metal hubs. The hubs screw together with 4-40 screws. One thing I do on these types of wheels is to remove all the screws and apply blue loctite and then re-assemble. The gear are air foiled so remember to mount with the thickest side pointing towards the front of the airplane. Bolt the gear to the fuse using the supplied bolts, lock nuts, and lock washers and remember to use a drop of loctite. Next install the gear plate with a bead of goop. After that, install the cuffs. They already come assembled with neoprene tubing around the openings and are made to be screwed to the gear legs however I lined them up, marked the gear, scuffed the gear with 80 grit paper and used goop to secure to landing gear. This will give a little more play in the event of a hard landing/gear flex and protect the side of the fuse as well as the cuffs from damage. Next thing was to install the supplied axles and wheel collars. This is a pretty standard installation by fitting the wheel pants for correct spacing and then grinding a flat spot on the axles for the collar set screws. Top it off with a little loctite and you should have a setup that will last for several years before requiring any maintenance. I also attached a J&J tailwheel I had laying around just so the tail can be off the ground, I'll get to the final install of this once I install the rudder.
Control Horns:
Usually when installing control horns, I take the time to seal the hinges. However, the Laser comes pre-hinged and sealed so this is a big plus. I do like to glue my own hinges so I know its right but these look great from the factory with very little gap and I'm able to get the throw that I need without any binding. The control horns supplied are composite. Again, no pics of this step but it is pretty straightforward and typical of any arf out there. Utilize some sand paper to scuff the areas of the control horn that insert into the control surface. Prepare the surface by removing the covering and test fit the control horns to the surface. I found that I had to clean some of the mounting holes a little bit with a small file in order to get the horns to seat all the way. I also mask around the area on the control surface to aid in clean up of any epoxy/glue that seeps out in the process. My glue of choice is Hysol for this step. Typically I use Hysol 9462 however I was out but had some E20HP that is a little quicker setup time and will still work great for this application. Using the hysol glue tip, shoot a little glue in the control surface and slide in your control horns. Take care to ensure the control horn centers above your hinge line and adjust during the dry fit if necessary to achieve this. I found that even with the tight fit of the control horns, they all came out dead center over the hingeline without any modifications. Once you have your control horn in the surface, screw a ball link in to keep the control horn straight and true. You will find two types of ball links included in the hardware, one will have a spacer which is for your servo arm and the other will not have a spacer and this is for your control horn.
A few other things to note:
While I had the glue gun out, I hit some problem spots on the canopy. The mounting tabs and carbon dowel rods on the front will eventually come loose on any plane, especially with a DA120 honking up front. So before that happens I usually re-enforce with some epoxy while I'm thinking about it. The first Slick I ever built, the canopy came apart on the third flight and I've seen numerous folks take off and do a pop top only to have their canopies fly off and its usually because the dowel rods up front have shaken loose. So this is a must and you should periodically check these areas when you're assembling at the field. I keep some 5 minute epoxy in the trailer for things such as this.
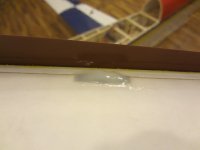