AKNick
640cc Uber Pimp
AJ 73" Laser 230z
Control Horn Installation.
As you can tell, I scuffed up the lower section pretty good of the control horn along with the underbelly of the plate with some sand paper just like the elevator joiner.. I even made a few notches with my dremel just cuz, heck it probably lowered its structural integrity for all I know ha!
I mixed up some 30min epoxy with some microbaloons to give it an almost pasty consistency. I think it helps keep the epoxy all in one place, and is supposed to lighten it up... but in retrospect your probably not saving THAT much weight. Anyways, dab it on all the contacting surfaces and the control horn slots, slap them together and wipe off the excess epoxy, then wipe clean with alcohol. Make sure the control surface has full travel before the epoxy sets up, one way to do it is to tape the control surface in the full deflection position and let it set up. Note that that ball link is temporarily installed to maintain the proper control horn separation.
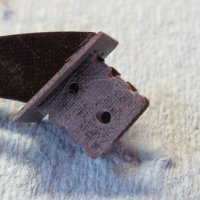
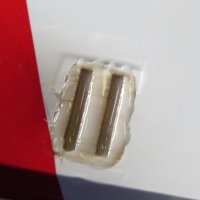
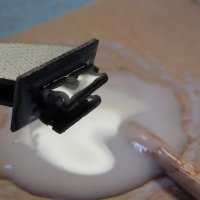
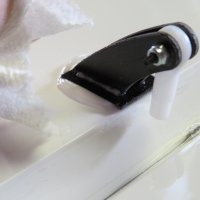
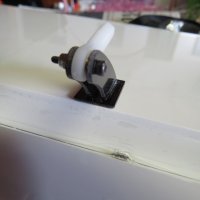
I don't think a tornado could even pull these horns out
Control Horn Installation.
As you can tell, I scuffed up the lower section pretty good of the control horn along with the underbelly of the plate with some sand paper just like the elevator joiner.. I even made a few notches with my dremel just cuz, heck it probably lowered its structural integrity for all I know ha!
I mixed up some 30min epoxy with some microbaloons to give it an almost pasty consistency. I think it helps keep the epoxy all in one place, and is supposed to lighten it up... but in retrospect your probably not saving THAT much weight. Anyways, dab it on all the contacting surfaces and the control horn slots, slap them together and wipe off the excess epoxy, then wipe clean with alcohol. Make sure the control surface has full travel before the epoxy sets up, one way to do it is to tape the control surface in the full deflection position and let it set up. Note that that ball link is temporarily installed to maintain the proper control horn separation.
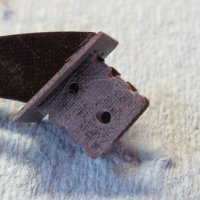
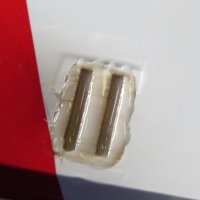
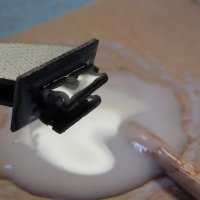
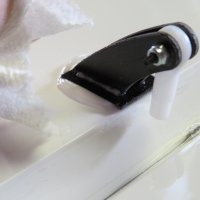
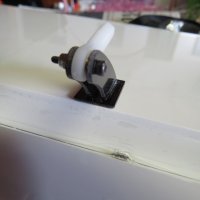
I don't think a tornado could even pull these horns out