AKfreak
150cc
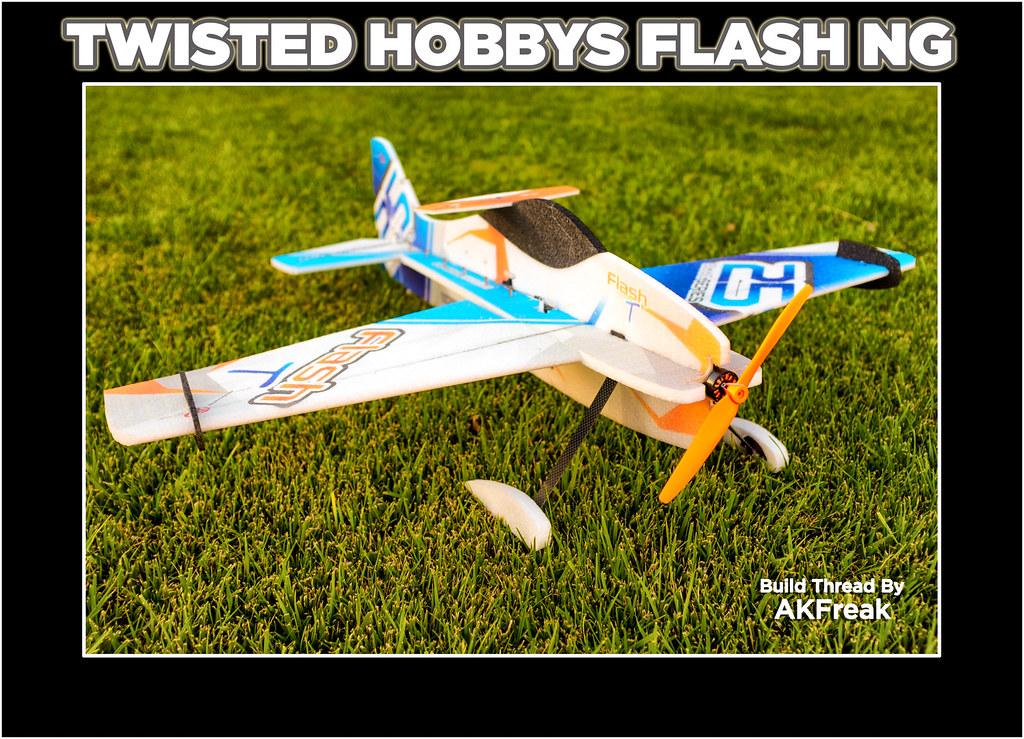
Twisted Hobbys / RC Factory's Brand New 36" EPP FLASH NG, "Official Build Thread"
This is the, "Official Build Thread" or the Twisted Hobbys / RC Factory's Brand New 36" EPP FLASH NG. All I can say is that I super excited to share this build with you folks, but before I start the build, I want to give a little of back story. As many of you know, I am a huge Twisted fan. I have built and own many TH planes, and I just love them. All of the planes I have owned each have a different personality, but share the one common trait,..... quality!
A week ago I was asked if I was interested in doing a build of a brand new line of planes from RC Factory. In case you don't know, RC factory is the place that brings the visions and projects of Twisted Hobbys to life. Well, I bet you guessed it by now, I said heck yes I would be interested in building the new design. This new design (36" inches) is bigger than the standard sized (32" inch) offerings from TH, but a little smaller than the new big dogs (39" inches) they just started offering not so long ago.
The Flash NG also knows as the Flash "T" should prove to be a great sized foamine to master 3D. At 36" inches it should do a little better in the wind than the 32" planes, but fit much easier than the new 39" planes. Another feature that sets this model apart is the fact it has Air foiled leading edges. That is to say the leading edge of the wings, and the horizontal stabilizer is radiused. Also the color is simply beautiful, and it's called. "the blue series".
Take a few minutes and watch this video below, as I offer to the world for the first time the all new, " 36" EPP FLASH NG"
[video=youtube_share;aJLkUfY52Qs]http://youtu.be/aJLkUfY52Qs?list=UUCa6sk3mAf6dT4wY9TYaNNg[/video]
I want to address how I am going to convey information in this build thread. Many people like written words and photos, while others prefer video. I like both depending on what platform I am on (PC, Phone or Tablet). So with that said, I will be offering the information in all forms. Remember some of the information will be repetitive, I just wanted you to know why. Any yeah, it's more work to present information in this way, but you guys are worth the effort
Lets Begin.
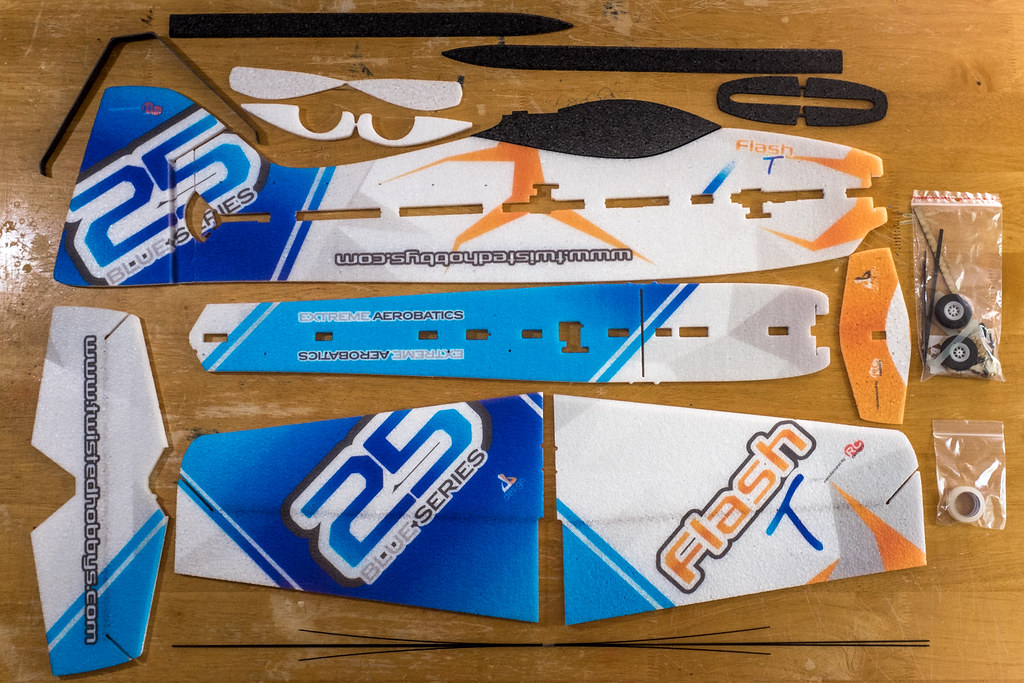
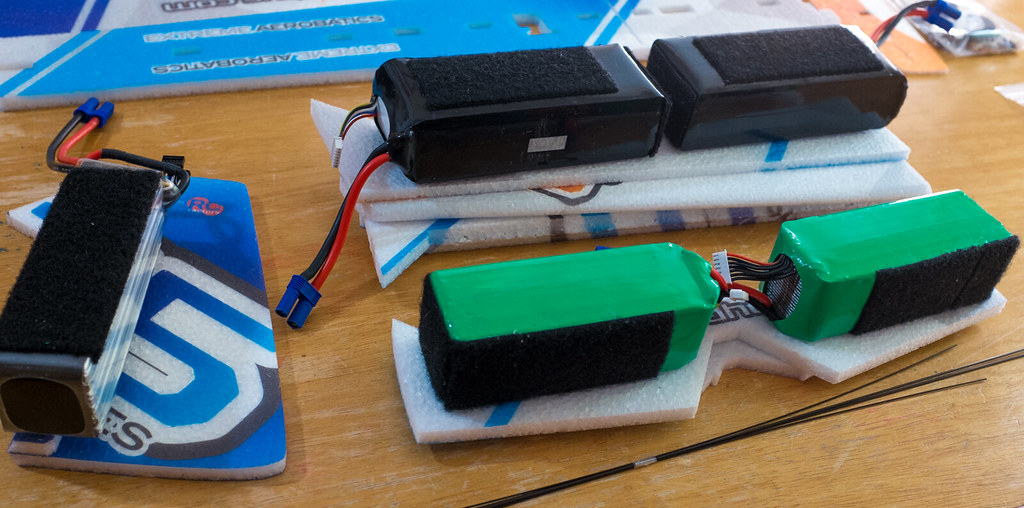
After you have gone through and inventoried the parts to make sure you have everything to build your new plane, the first step is to weigh down all of the control surfaces for 24-48 hours. This will help deal with any memory issues that the foam retains at the hinge points. This memory will cause the servos to work too hard (and they will burn up). Also you wont achieve a full or equal throws which can cause major performance issues. You got the best model, you need to insure it will fly as it was intended.
Video Quick Tip
[video=youtube_share;t50fMxICiWs]http://youtu.be/t50fMxICiWs?list=UUCa6sk3mAf6dT4wY9TYaNNg[/video]
Tools You May Need
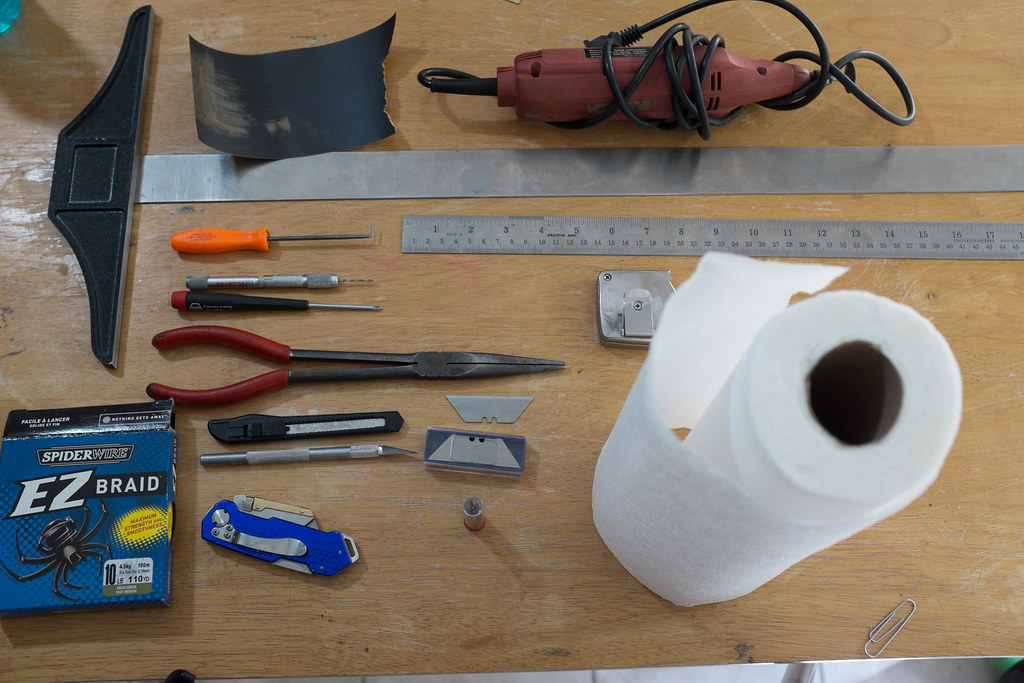
Before you build the plane, you may want to collect all the tools you will need to complete the job. You will need a Sharp Razor Knife of some sort. You will also need a drill, some sand paper, some pliers, a long metal straight edge, a pick, a tape measure, and possibly a dremel tool to cut the carbon fiber control rods.
[video=youtube_share;N4_zAPAnxLc]http://youtu.be/N4_zAPAnxLc[/video]
"Welders Glue"
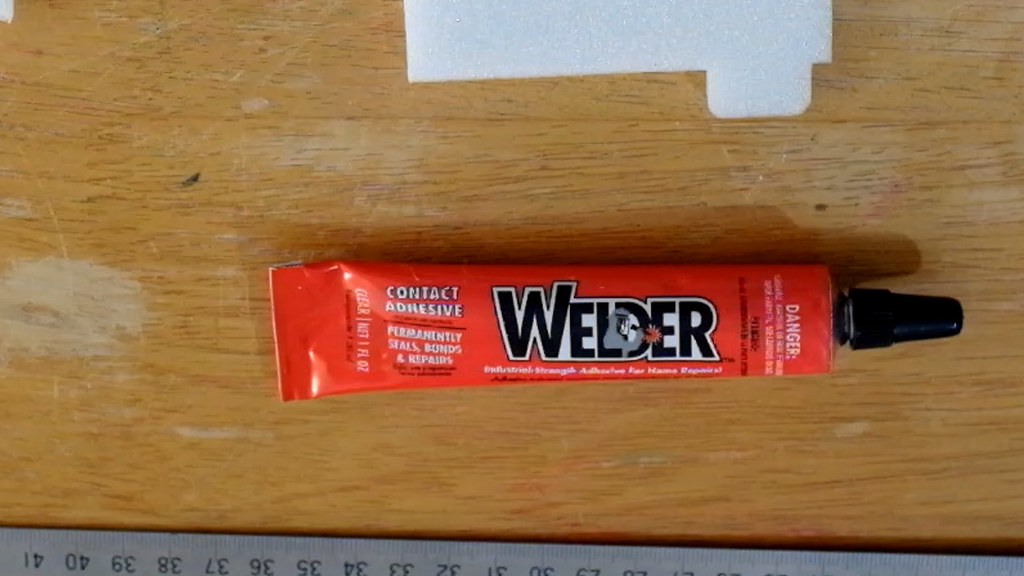
The Glue we will be using to build this plane is called, "Welders". You can get it when you buy your kit from Twisted Hobbys. This glue is contact cement and works pretty good on EPP foam. Welders is kind of hard to find at the hardware store, and for $5 bucks, like I said you get two tubes from Twisted. There are several ways you will have to use this type of glue. One way is the recommended way, as a contact cement. You apply glue to the both surfaces that are going to be bonded. Press them together, then pull them apart, then let them dry for 5 to 10 mins. Once this stuff dries, then it is pressed back together, it stays stuck very well. However there are times when you need to shift parts around, this is when you need to use the, Wet" method of working with this glue. Welders can also be used to make control surface hinges. Welders is pretty neat stuff, and it has been used for a long time to build foam models.
[video=youtube_share;fl6yBs_IfR4]http://youtu.be/fl6yBs_IfR4[/video]
Setting Up, Cutting & Insalling The Wooden Spar Strip
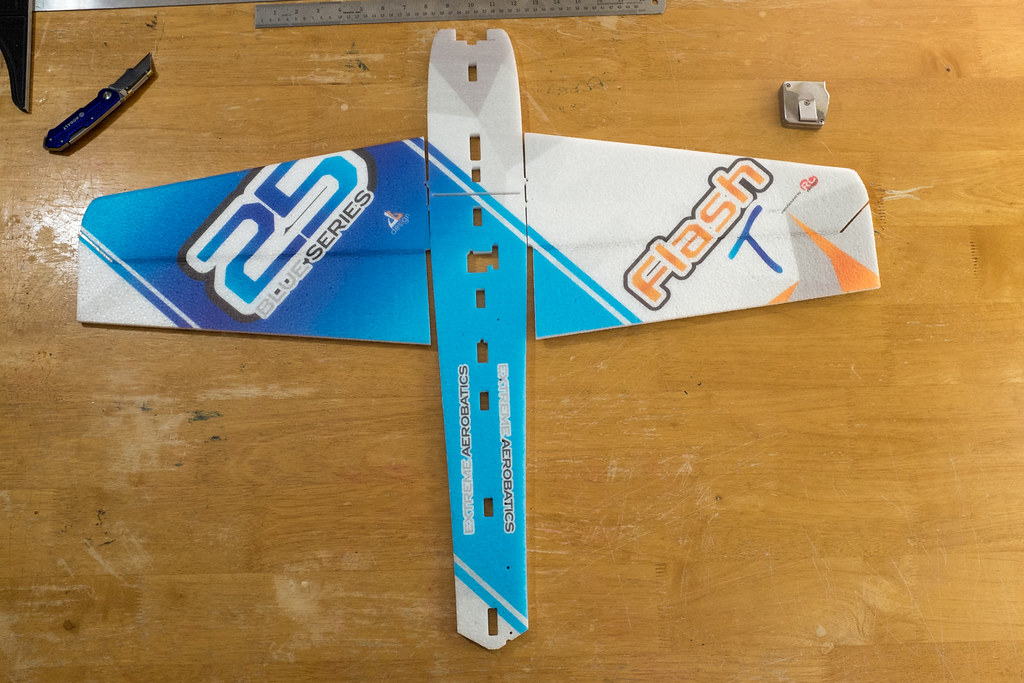
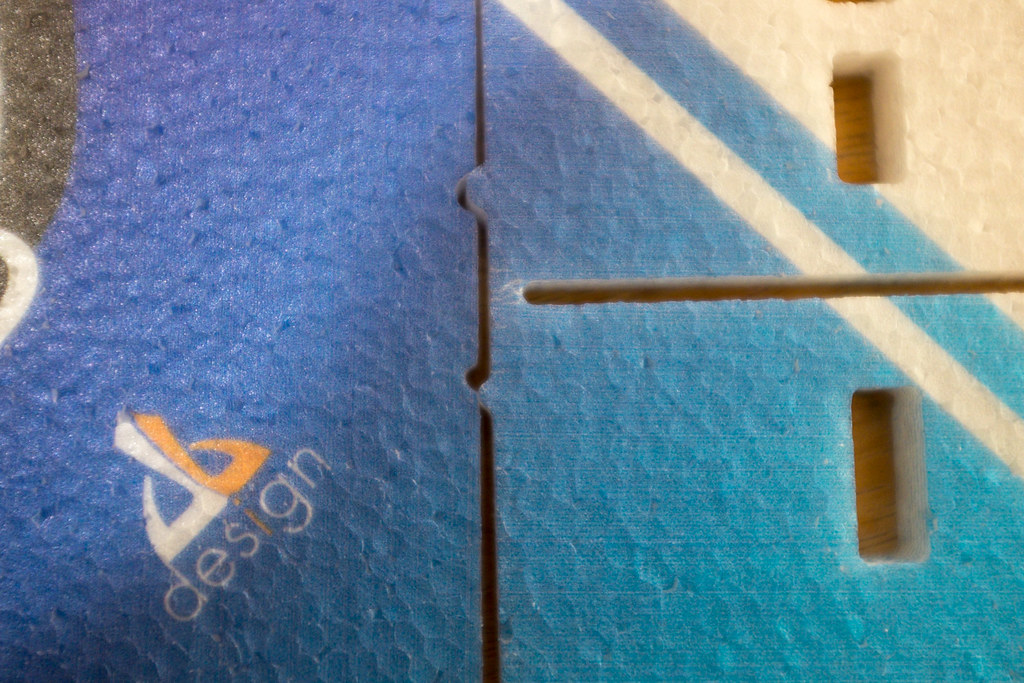
When you put you wings and Horizontal fuse on the build table, you will quickly realize that the Wings and the Fuse registering table don't line up. The first time I built this type of model from TH/RCF, I was scratching my head because I didn't realize you need to cut the horizontal fuselage in to two pieces. (I hate directions

So, grab your metal strait edge and a sharp razor knife and split the horizontail fuse into to pieces, then use the straight edge to trim off the resulting tabs, so you end up with a front and back horizontal fuselage sections that will butt flush against each other.
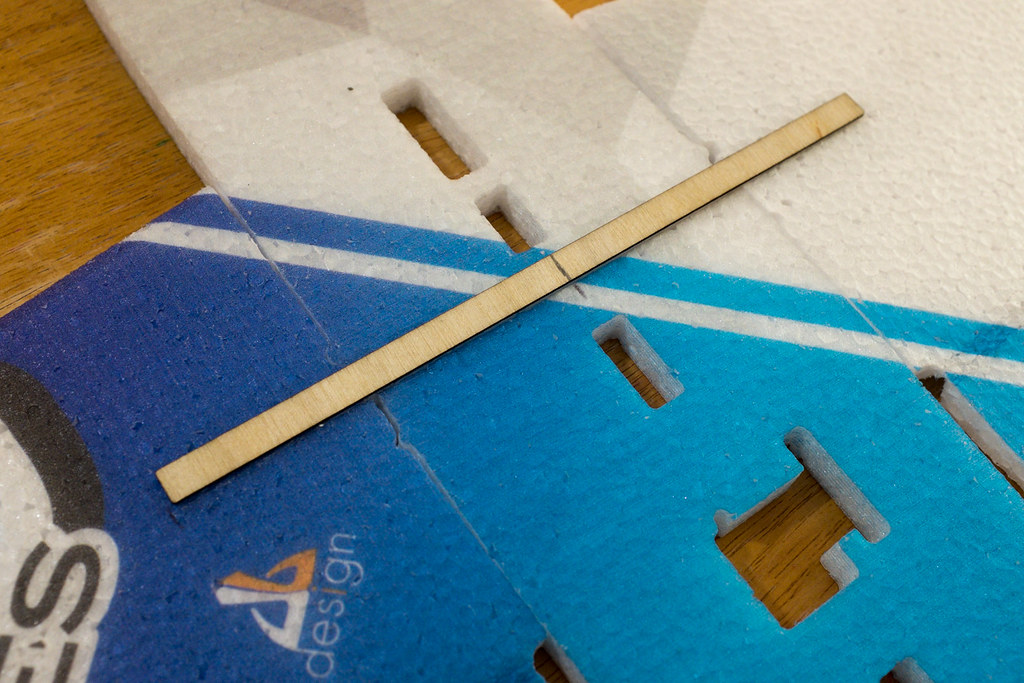
Now you need to fit the wings and horizontal fuse parts together, and grab the wooden spar strip. On the strip,you need to measure and mark center. Also mark center on the horizontal fuse section. Then line up the mark on the spar strip with the mark on the horizontal fuse. In doing so, you have just registered the wooden spar.
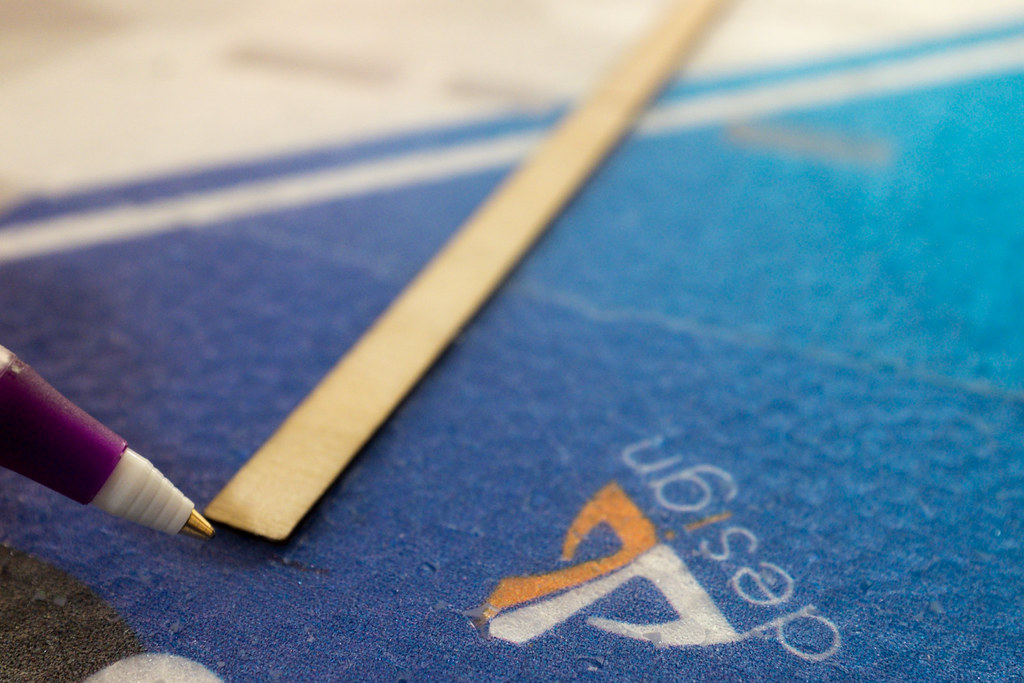
Now you need to make marks on the outside of the spar. Make the marks on both the left and right wing, these marks will serve as the stopping point when you make your cuts to install the spar to the wings.
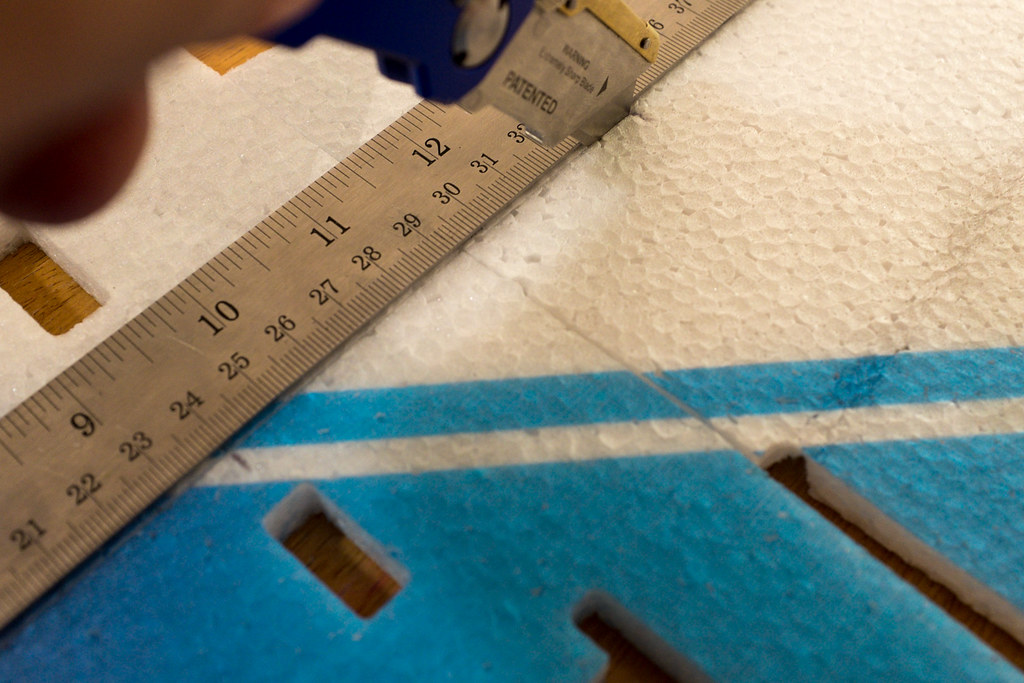
Now, with the wings firmly pressed into place against the front and back horizontal fuselage, lay your metal straightedge across the both wings with the straightedge parallel with the cut in the front and back horizontal fuselage (wow that was a mouth full). Take notice of where you make the marks on the wings. These marks are the stopping points for the cut you are about to make. Using a sharp razor, make a cut all the way through both the left and right wing, again stopping at your marks.
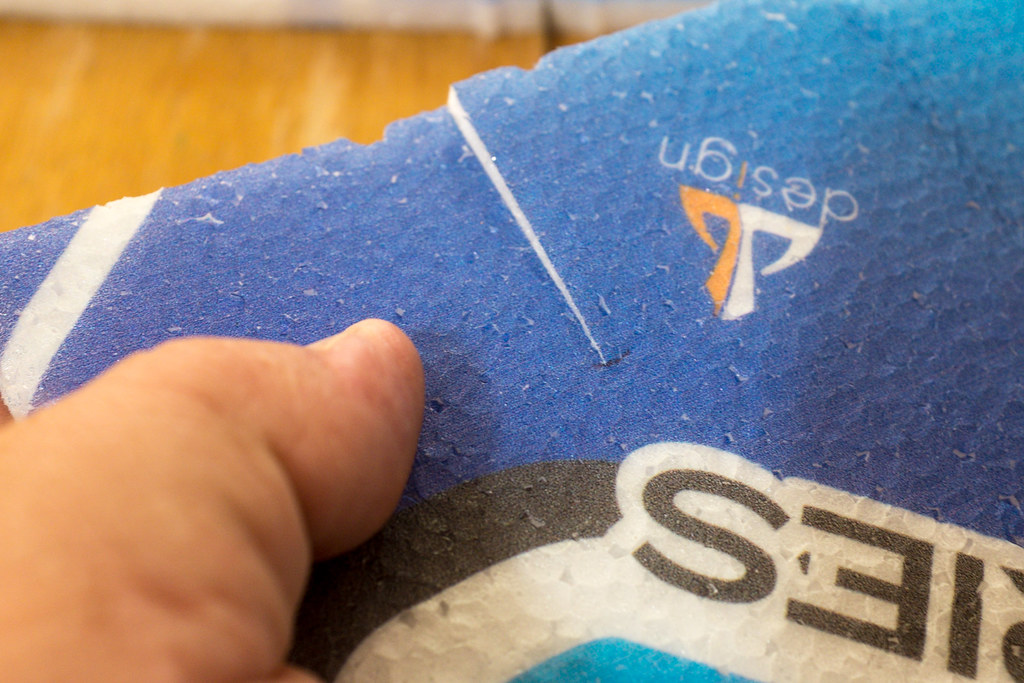
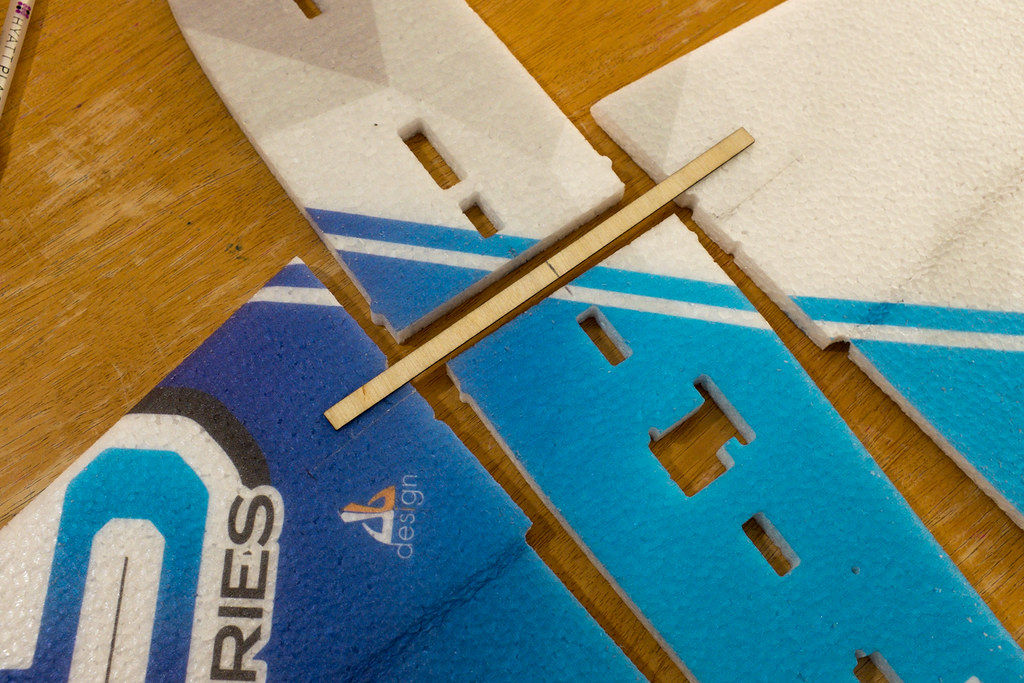
When your cuts are done, this is what it will like.
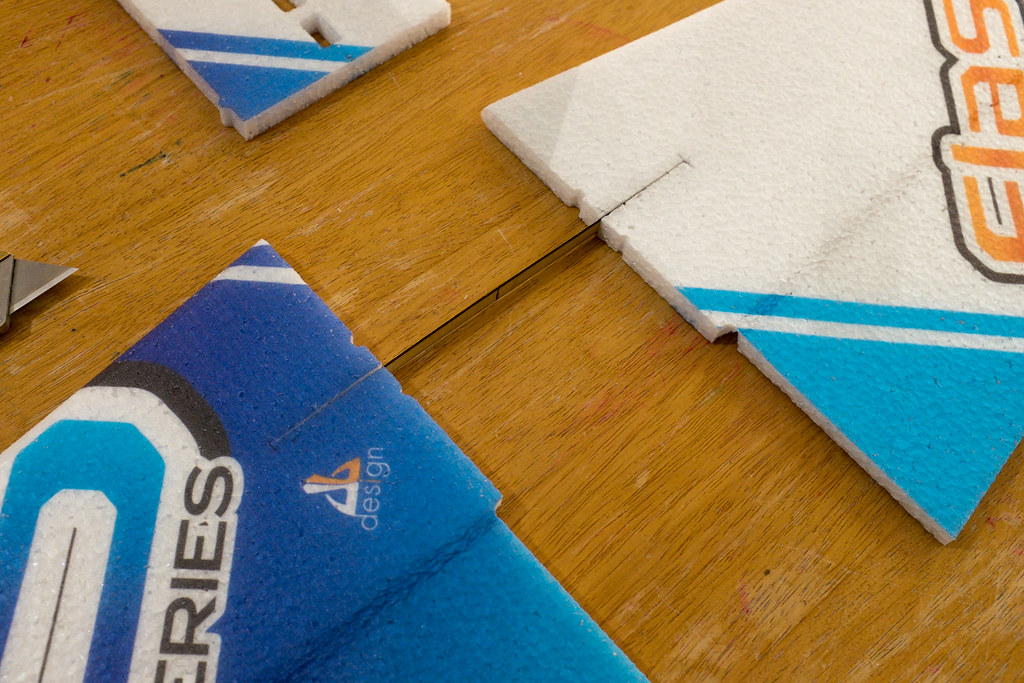
Now you want to fit the wooden spar, make sure it's pressed up against the marks on the wings. Now slip in the front and back of the horizontal fuselage, making sure everything is nice and tight. Remember we aren't gluing anything until everything is fitted, including the top and bottom Carbon Fiber Spars.
Video Summary
[video=youtube_share;gBDdtKAL3aU]http://youtu.be/gBDdtKAL3aU[/video]
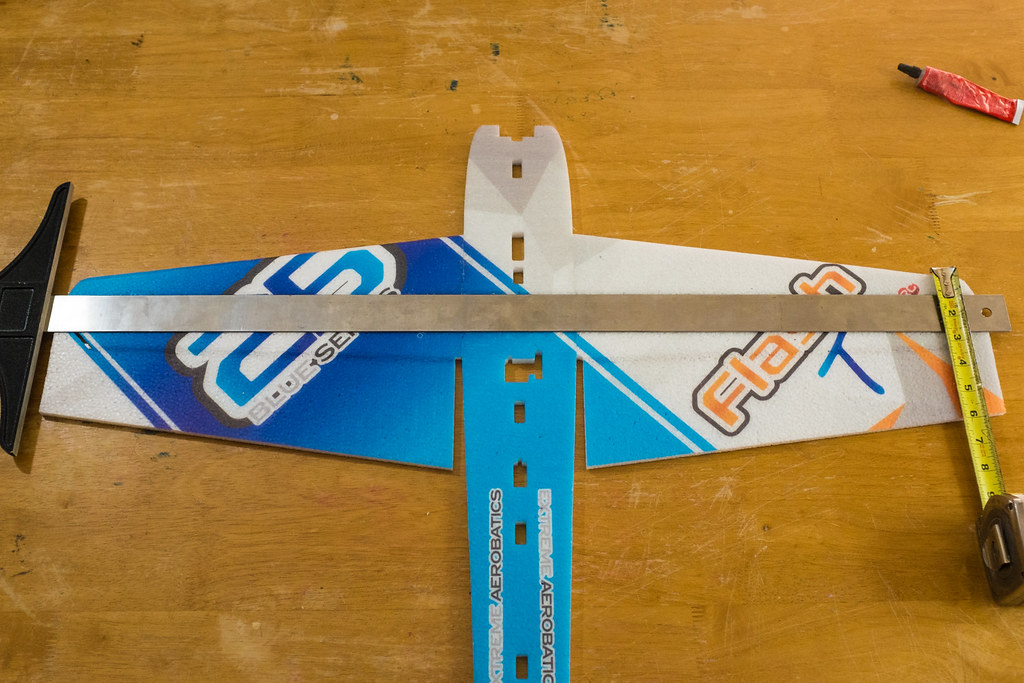
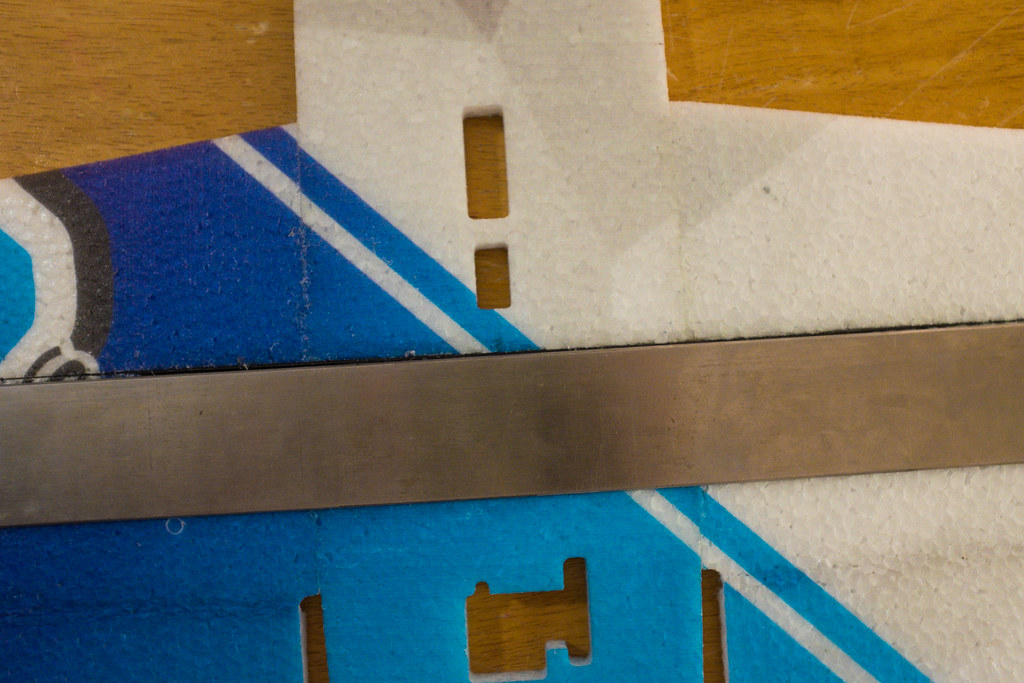
Now, with everything nice and tightly fitted, lay your long metal straight edge across the wings. make sure it is parallel and centered on the wooden spar strip.
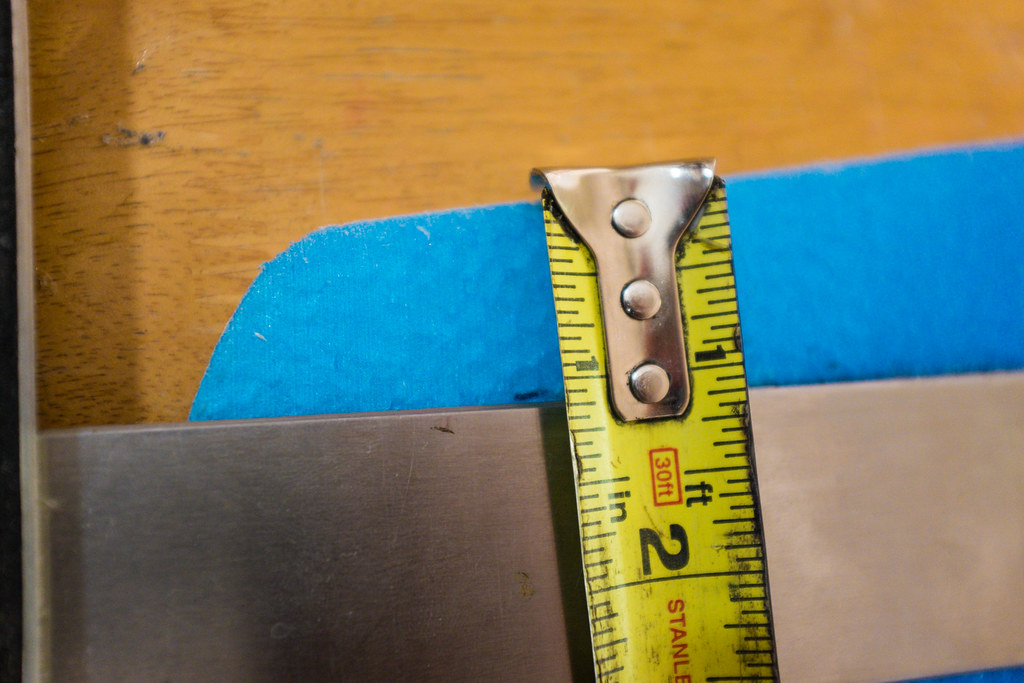
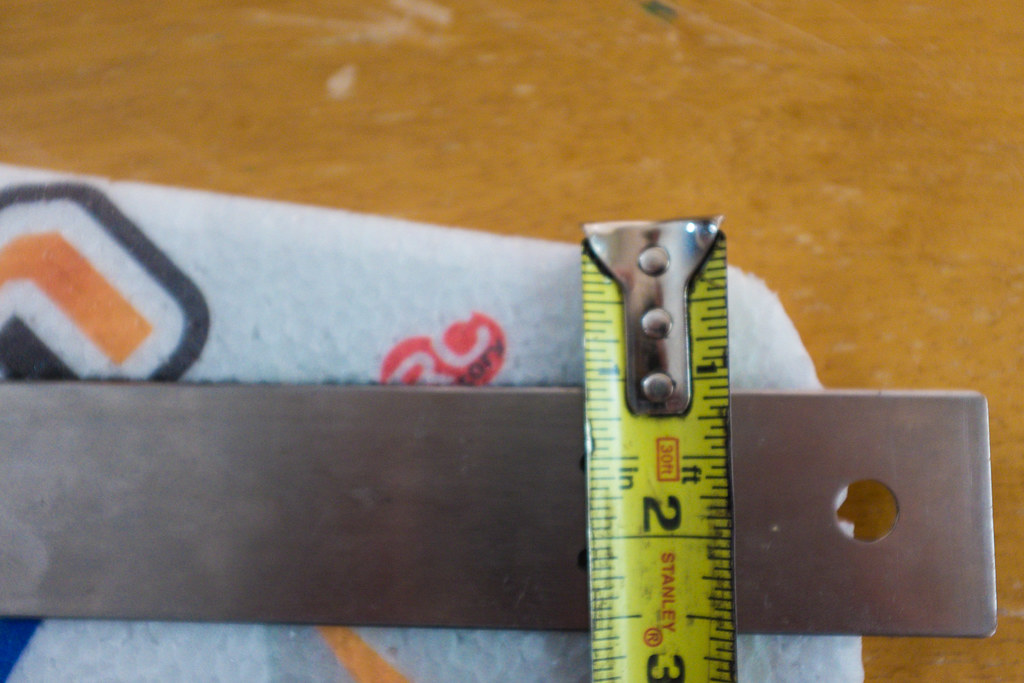
With all of the pieces firmly pressed into place, and the straightedge laying on top of the center and parallel to the wood spar strip, measure and mark 1" inch down from the leaden edge of the wing on both sides. These marks will keep you lined up correctly when you make your main spar cuts. Also lay up the carbon fiber spar, just to measure it from side to side to make sure it's in the center of the wing span from left to right. I took note on the yard stick so I would know when to stop my cut. (see the video for a visual explanation)
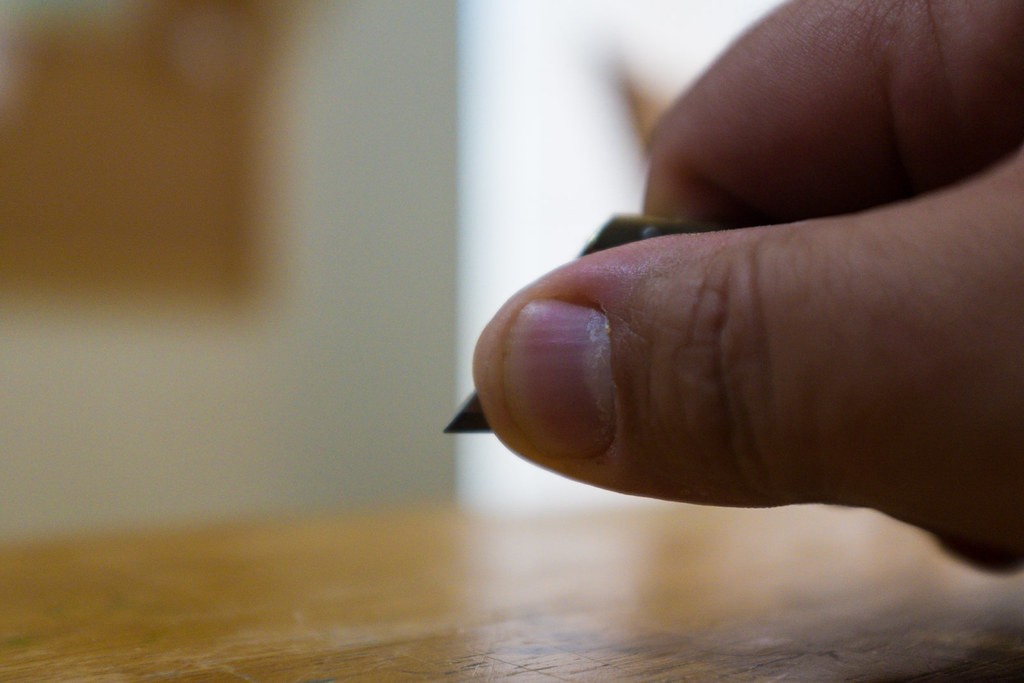
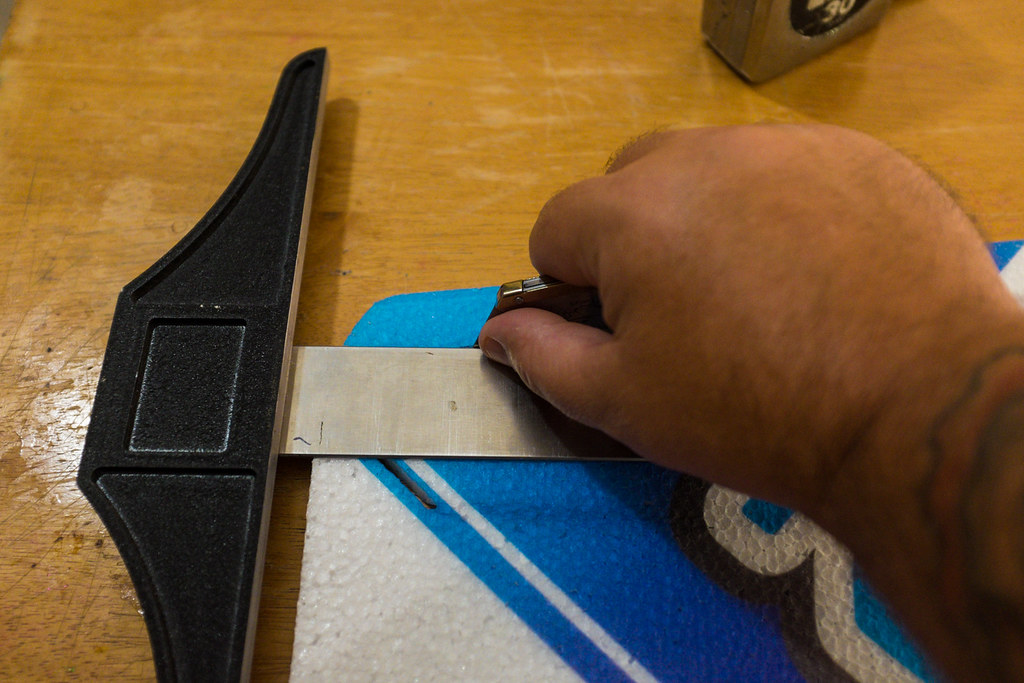
When you make your cut to embed the carbon fiber spar, you want to be careful not to go to deep. I use my thumb as a guide to rest on the straight edge. For that reason, I like to use a standard utility knife to make these types of cuts. The idea here is to just cut deep enough so the carbon fiber spar sits flush (or slightly below) with the surfaces of the wing. Be careful and make your cuts, stopping at the end where the spar stops. Then flip the plane over and repeat the process. Just be careful, take your time, and make sure everything is nice and tight before you make your cuts.
Video Tip, Embedding the Top & Bottom Spars
[video=youtube_share;stt_25zPwsU]http://youtu.be/stt_25zPwsU?list=UUCa6sk3mAf6dT4wY9TYaNNg[/video]
The Bottom Spar Install
[video=youtube_share;bbvtaNEJRwg]http://youtu.be/bbvtaNEJRwg[/video]
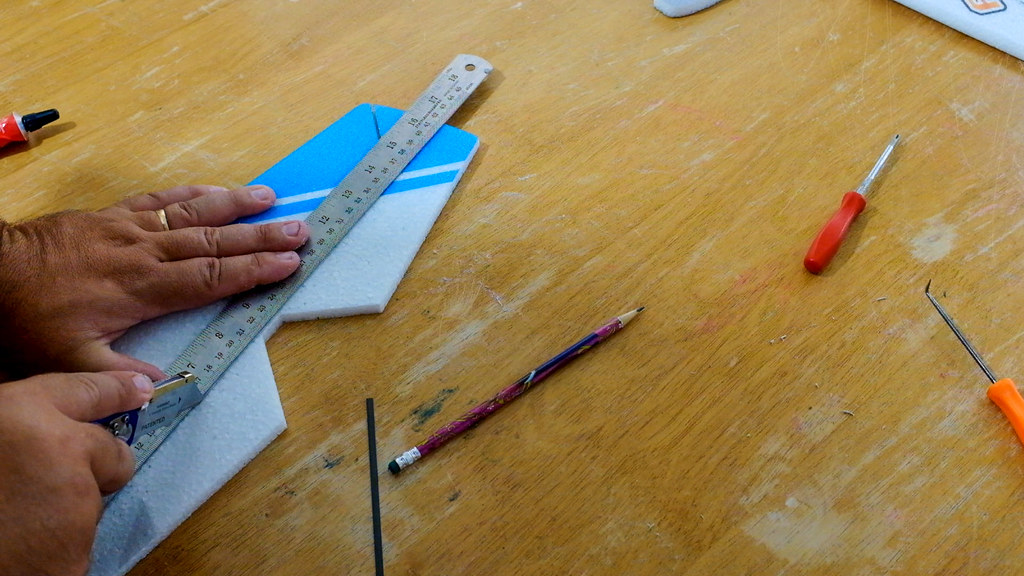
The Next step is to install the carbon fiber reinforcement strip into the base of the horizontal stabilizer (the elevator). Just use a straight edge, and a sharp razor to open the pre-existing slot placed by the factory. When you glue in the carbob strip, be sure to rough up the surfaces with 120-150 grit sand paper. Also when you glue the seams andthe strip, we want to use the wet method of gluing with welders. Well not exactly wet, but semi wet. Glue up all of the surfaces, then install the CF strip. Then remove it, and let the glue tack up for 2-3 mins. If you let the glue dry to the touch, it's very difficult to install the carbon strip. You need to be able to shift the strip into place, much like you did with the main spars.
Tips to Install the Carbon Fiber Reinforcement Strip
http://youtu.be/8kQND52WvPM?list=UUCa6sk3mAf6dT4wY9TYaNNg
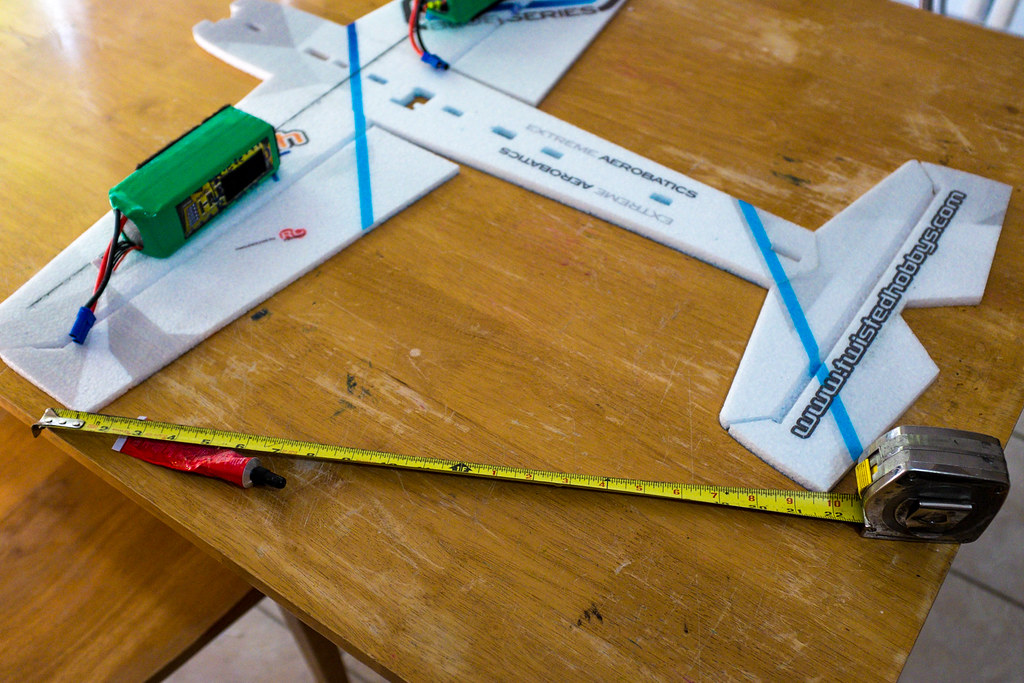
Attaching The Horizontal Stabilizer/Elevator To The Fuse
Now its time to attach the horizontal stabilizer to the fuselage. You need to use a tape measure of some sort to insure the tail is square to the wings, and you need to make sure the horizontal stab is flush to the top of the horizontal fuselage. When gluing the stab to the fuse, you need to use the dry method of welders glue.
I find flipping the wings/fuselage so the top side is facing down to be the easiest way to install the horizontal stabilizer. I say this because this will insure the fuselage is flush with the horizontal stabilizer. If you glue the stabilizer on flush to the bottom of the horizontal fuselage, the lower vertical fuselage will have a gap when you try to install it because the horizontal fuselage and the horizontal stab are two different thicknesses.
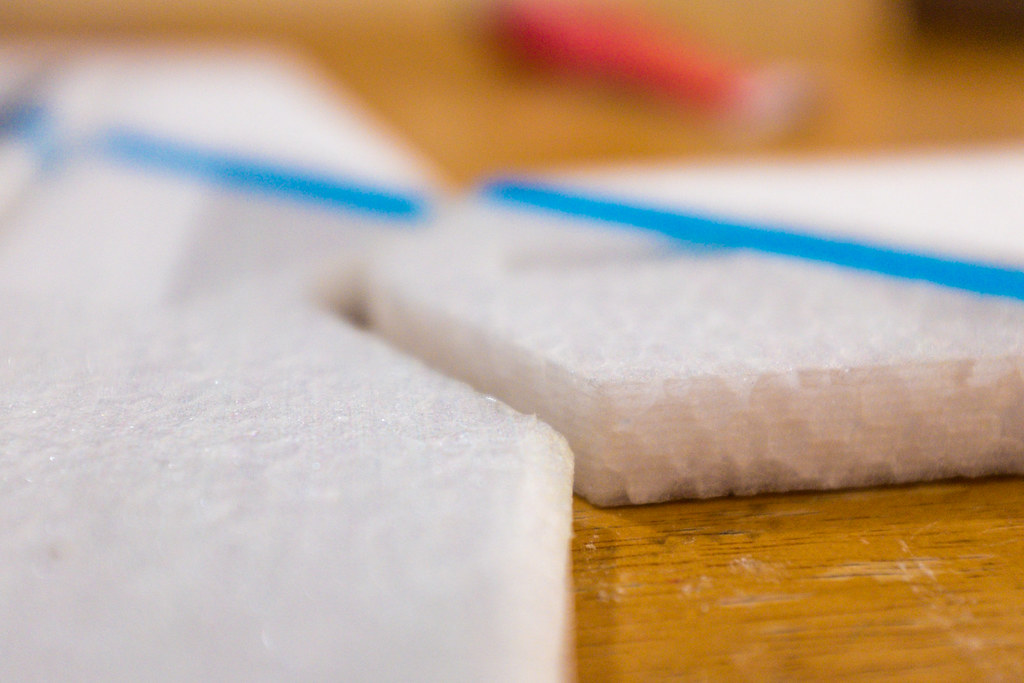
Video Tips To Attach The Horizontal Stabilizer To the Horizontal Fuselage
[video=youtube_share;1R_-B1ptbTE]http://youtu.be/1R_-B1ptbTE[/video]
Last edited by a moderator: