That nasty four letter word "Work" has been getting in the way, but I did manage to prime a few of the test panels I've been working on. Some of them I sprayed with two coats of Nason 421-19 2K urethane primer with Nason 483-87 activator. I reduced the activated primer by about 10% with Nason 441-21 reducer to make it lay a little smoother.
Two others I sprayed with a thin self-etching primer. The self-etch doesn't fill any thing but it will show any pinholes or bad spots and you can spray basecoat right over it if you want. I have two more that I'm going to spray with epoxy primer, but I was out of it the night I sprayed these.
I sanded the best two panels, one with urethane primer and one with self-etch, with 400 dry and weighed them. Before I would paint I would wet sand it with 600, but for testing this is close enough.
Both panels are slick, smooth, pinhole free and would be great painted. Here is a short rundown of the weight gains on these two parts.
Urethane primed part:
Weight after cloth and 1st coat of resin, sanded. 0.30 ounces
Weight after 2nd coat of resin, sanded. 0.30 ounces (no measurable gain of weight for the second coat of resin after sanding)
Weight after priming and sanding. 0.33 ounces
Self-Etch primed part:
Weight after cloth and 1st coat of resin, sanded. 0.32 ounces
Weight after 1 coat of joint compound, sanded. 0.33 ounces (I tried a coat of joint compound between the first and second coat of resin)
Weight after 2nd coat of resin, sanded. 0.33 ounces
Weight after 3 coats of Self Etch primer. 0.34 ounces
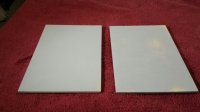