Capt.Roll
70cc twin V2
I’ve started the assembly of my new 30% OMP Extra 300 mid-wing ARF. I’m on vacation thru Jan 6th and should have ample opportunity to work on the Extra along with some maintenance on my 100cc Yak SP-55M and 71” electric Slick. It would be nice to have this project completed and ready to maiden should there be some decent flying weather sometime in the next six weeks. For sure want to have the Extra ready to go by March 1st.
Picked up the two shipping boxes (fuse & wings) from the Greyhound terminal the week after Thanksgiving. The outer cartons were heavy corrugated cardboard and seemed to provide ample protection (at least for Greyhound handling) to the inner cartons and ARF components. I did a quick inspection on the Greyhound dock and everything inside was neatly packed, secured from bouncing around, arrived with no obvious visible damage and all parts and pieces present.
The first thing I usually do is take a sealing iron and go over all the covering and iron out any wrinkles that may have developed and to make sure all the edges are sealed. The covering on this ARF was nicely done; there were some wrinkles but the edges and curved surfaces were cut clean and sealed tight. The trim pieces on the fuse/rudder and top/bottom of the wings, stabilizer and elevators have nice symmetry and clean lines as well. The one area that is a little sloppy is where the vertical stabilizer and fuse come together; that is a tough compound curve to work and have the covering fit in there clean. There is room for improvement here.
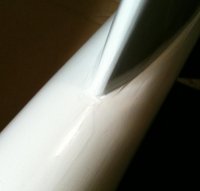
On my gas planes I also like to seal the firewall, motor box and fuel deck with Spar varnish. It does a nice job sealing the wood but will still allow the wood to breath with changes in temperature and humidity. The Spar varnish also seems to be resistant to gas/oil spills and exhaust residue.
After the Spar varnish I paint the firewall and motor box with Rust-oleum Multicolored Textured spray paint. Even though it’s covered by the cowl I like the look of the uniform color; it’s available in several colors, I like the dark gray. It’s also very resistant to gas and oil.
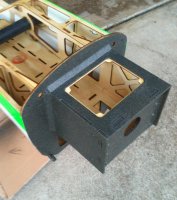
Picked up the two shipping boxes (fuse & wings) from the Greyhound terminal the week after Thanksgiving. The outer cartons were heavy corrugated cardboard and seemed to provide ample protection (at least for Greyhound handling) to the inner cartons and ARF components. I did a quick inspection on the Greyhound dock and everything inside was neatly packed, secured from bouncing around, arrived with no obvious visible damage and all parts and pieces present.
The first thing I usually do is take a sealing iron and go over all the covering and iron out any wrinkles that may have developed and to make sure all the edges are sealed. The covering on this ARF was nicely done; there were some wrinkles but the edges and curved surfaces were cut clean and sealed tight. The trim pieces on the fuse/rudder and top/bottom of the wings, stabilizer and elevators have nice symmetry and clean lines as well. The one area that is a little sloppy is where the vertical stabilizer and fuse come together; that is a tough compound curve to work and have the covering fit in there clean. There is room for improvement here.
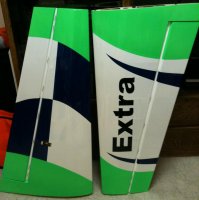
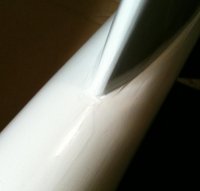
On my gas planes I also like to seal the firewall, motor box and fuel deck with Spar varnish. It does a nice job sealing the wood but will still allow the wood to breath with changes in temperature and humidity. The Spar varnish also seems to be resistant to gas/oil spills and exhaust residue.
After the Spar varnish I paint the firewall and motor box with Rust-oleum Multicolored Textured spray paint. Even though it’s covered by the cowl I like the look of the uniform color; it’s available in several colors, I like the dark gray. It’s also very resistant to gas and oil.
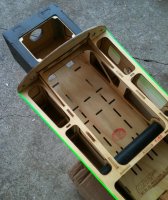
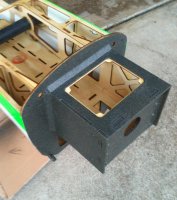