Question on the airman wheels normally the axel come with an E clips as you have described but then you stated that install a bolt into the end, does the axel come with threaded hole on the end if not how did you do that.
Hey Snoops... "c"/"e" clip... all the same to me. If they don't make a complete circle they usually get what ever name I choose to call them. Lol. Seriously, the axles come pre-drilled and tapped when you get them. One of the reasons I have gone specifically to them over any other axle.
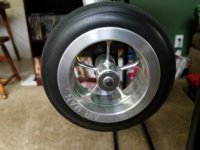
The only planes I have, (Hangar 9 Sukhoi and Pilot Edge) are the only planes without the White Rose axles or aluminum wheels. I have them, just no time to swap it seems.
I would like to ask for some advice. I built a AMR Stick a year ago, the Stick has 150 on the front and the weight is 40 lbs ready to take off, and have nothing but problems with the landing gear axles. The first set axels failed just taxing the plane for first time at the field. At the time I thought cheap Chinese steel. So replace the axels with 1/4 socket head screws. They worked but after the first landing they were bent. So replace the the axels with 3/8 socket head bolts and replaced the wheels with 8 inch diameter wheelsr from the 6 inch diameter wheel. Did about 10 flights with the plane and everything was great until yesterday. Came in for a landing and honestly it was good landing no bounce just a normal landing, as the plane landed both wheels snapped off landing gear bug in and flipped the plane and the two wheels rolled down the field, I was just absolutely dumb founded. I do not know what to do. It just does not make any sense it should be impossible to snap off two 3/8 bolts simultaneously like that.
This is very odd to me. It is very hard for me to understand how a 40 lb plane is bending Axel's including the Big Bolt you have been putting in. Back approximately 5 years ago I did bend a set of white rose axles that were on my 260. Not severely, however enough that I could see once the plane was brought in that I had bent them. It was due to a very rough Landing. Since then, I have not had not one set of bent axles on any of my planes. Even my big Yak and my son's big Edge come in at over 50 pounds with fuel. We don't have any problems with bent axles on those planes. My guess is that the reason the wheels broke off is because when you drilled for the 3/8 bolt you took out too much meat on the landing gear and weakened the main absorption area, therefore too much forward load or sideload snap the landing gear. I really wish I could offer you something that would be helpful. In the photos that I have attached, you will see on my big Yak wheels that I am using, the same axles on it as I do all my other planes. No matter what size it may be. Would really like to know what you figure out on this dilemma.