Ohio AV8TOR
Just Do It
So I am getting close to that spot on my 91" Extra build that I need to think about if I am going to split my cowl or not. Right now I am unsure of the baffles. I have drawn up in CAD unique baffles that blend from the inlet to the exact size of the cylinder. Looking straight in from the front last night much of the cylinder is below the inlet line requiring the blend to blend down as you can see from the pictures below. I am going to print these in RP. So with baffles like this is it best to simply bond this to the lower half only or split the baffles as well having a top and bottom half.
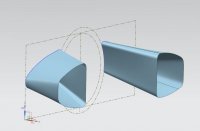
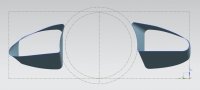
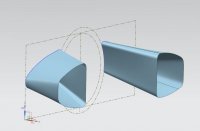
Last edited: