I struggled quite a bit to find the best geometry for the ailerons. The ball links would bind against the servo arm and/or the control horn.
Bevel to bevel is 55 degrees. Most of us know that anything beyond 38 degrees slows down the roll rate and is just drag. Keeping that in mind I always like the surface to be able to travel bevel to bevel. My solution is this:
1.5” NWRC arm using the furthest outboard hole.
middle hole on the control horn.
endpoints are approx 90-110 to reach 38 degrees.
this accomplishes two things. Best servo resolution as I am allowing the servo to travel basically 100%
Last is geometry, using a smaller servo arm, and the middle hole of the control horn the linkage stays mostly parallel to its surface exempt at neautral which is perfect. 3D planes with large torque can get away with less than parallel linkages at neutral as there isn’t much load on it there. It’s at deflection what matters.
I originally posted in a FB skywing owners group a question about how other people had set up their 89” SW lasers and it turned into more of a deflection thread about everyone saying 38degrees is all you need. Gotta love it when folks don’t understand the question or own the plane and make an uneducated guess to prove they know something.
Had a few PMs from people trying to help me that actually owned the plane but said they didn’t want to hurt anyone’s feelings publicly LOL. Got the information and help I needed, but it was painful. LOL!
I’d come home from night shift trying to figure it out and left me dumbfounded. I tried different arms and settings but this was the best result.
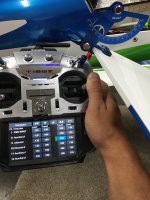